CIRCULAR PITCH (CP)The length of the arc of
the pitch circle between the centers or corresponding
points of adjacent teeth.
ADDENDUM (A)The height of the tooth above
the pitch circle or the radial distance between the pitch
circle and the top of the tooth.
DEDENDUM (D)The length of the portion of the
tooth from the pitch circle to the base of the tooth.
CHORDAL PITCHThe distance from center to
center of teeth measured along a straight line or chord
of the pitch circle.
ROOT DIAMETER (RD)The diameter of the
circle at the root of the teeth.
CLEARANCE (C)The distance between the
bottom of a tooth and the top of a mating tooth.
WHOLE DEPTH (WD)The distance from the
top of the tooth to the bottom, including the clearance.
FACEThe working surface of the tooth over the
pitch line.
THICKNESSThe width of the tooth, taken as a
chord of the pitch circle.
PITCH CIRCLEThe circle having the pitch
diameter.
WORKING DEPTHThe greatest depth to which
a tooth of one gear extends into the tooth space of
another gear.
RACK TEETHA rack may be compared to a spur
gear that has been straightened out. The linear pitch of
the rack teeth must equal the circular pitch of the mating
gear.
HELICAL SPRINGS
There are three classifications of helical springs:
compression, extension, and torsion. Drawings seldom
show a true presentation of the helical shape; instead,
they usually show springs with straight lines. Figure
4-15 shows several methods of spring representation
including both helical and straight-line drawings. Also,
springs are sometimes shown as single-line drawings as
in figure 4-16.
FINISH MARKS
The military standards for finish marks are set forth
in ANSI 46.1-1962. Many metal surfaces must be
finished with machine tools for various reasons. The
acceptable roughness of a surface depends upon how the
Figure 4-15.Representation of commm types of helical
springs.
Figure 4-16.Single line representation of springs
part will be used. Sometimes only certain surfaces of a
part need to be finished while others are not. A modified
symbol (check mark) with a number or numbers above
it is used to show these surfaces and to specify the degree
of finish. The proportions of the surface roughness
symbol are shown in figure 4-17. On small drawings
the symbol is proportionately smaller.
The number in the angle of the check mark, in this
case 02, tells the machinist what degree of finish the
surface should have. This number is the
root-mean-square value of the surface roughness height
in millionths of an inch. In other words, it is a
measurement of the depth of the scratches made by the
machining or abrading process.
Wherever possible, the surface roughness symbol is
drawn touching the line representing the surface
Figure 4-17.Proportions for a basic finish symbol.
to
4-6
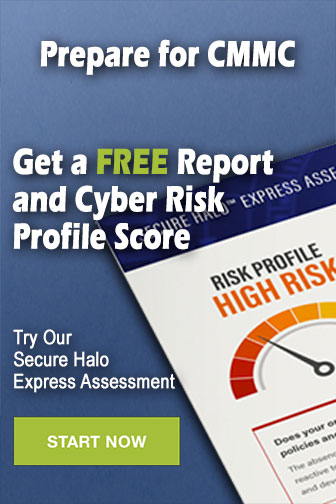