View A shows the lateral, or curved, surface of a
cylindrically shaped object, such as a tin can. It is
developable since it has a single-curved surface of one
constant radius. The width of the development is equal
to the height of the cylinder, and the length of the
development is equal to the circumference of the
cylinder plus the seam allowance.
View B shows the development of a cylinder with
the top truncated at a 45-degree angle (one half of a
two-piece 90-degree elbow). Points of intersection are
established to give the curved shape on the
development. These points are derived from the
intersection of a length location, representing a certain
distance around the circumference from a starting point,
and the height location at that same point on the
circumference. The closer the points of intersection are
to one another, the greater the accuracy of the
development. An irregular curve is used to connect the
points of intersection.
View C, shows the development of the surface of
a cylinder with both the top and bottom truncated at
an angle of 22.5° (the center part of a three-piece
elbow). It is normal practice in sheet metal work to
place the seam on the shortest side. In the
development of elbows, however, the practice would
result in considerable waste of material, as shown in
view A. To avoid this waste and to simplify cutting
the pieces, the seams are alternately placed 180° apart,
as shown in figure 8-13, view B, for a two-piece
elbow, and view C for a three-piece elbow.
RADIAL-LINE DEVELOPMENT OF
CONICAL SURFACES
The surface of a cone is developable because a thin
sheet of flexible material can be wrapped smoothly
about it. The two dimensions necessary to make the
development of the surface are the slant height of the
cone and the circumference of its base. For a right
circular cone (symmetrical about the vertical axis), the
developed shape is a sector of a circle. The radius for
this sector is the slant height of the cone, and the length
around the perimeter of the sector is equal to the
circumference of the base. The proportion of the height
to the base diameter determines the size of the sector, as
shown in figure 8-14, view A.
The next three subjects deal with the development
of a regular cone, a truncated cone, and an oblique
cone.
Regular Cone
In figure 8-14, view B, the top view is divided into
an equal number of divisions, in this case 12. The
chordal distance between these points is used to step off
the length of arc on the development. The radius for the
development is seen as the slant height in the front view.
If a cone is truncated at an angle to the base, the inside
shape on the development no longer has a constant
radius; it is an ellipse that must be plotted by establishing
points of intersection. The divisions made on the top
view are projected down to the base of the cone in the
front view. Element lines are drawn from these points
to the apex of the cone. These element lines are seen in
their true length only when the viewer is looking at right
angles to them. Thus the points at which they cross the
truncation line must be carried across, parallel to the
base, to the outside element line, which is seen in its true
length. The development is first made to represent the
complete surface of the cone. Element lines are drawn
from the step-off points about the circumference to the
center point. True-length settings for each element line
are taken for the front view and marked off on the
corresponding element lines in the development. An
irregular curve is used to connect these points of
intersection, giving the proper inside shape.
Truncated Cone
The development of a frustum of a cone is the
development of a full cone less the development of the
part removed, as shown in figure 8-15. Note that, at all
times, the radius setting, either R1 or R2, is a slant height,
a distance taken on the surface of the cones.
When the top of a cone is truncated at an angle to
the base, the top surface will not be seen as a true circle.
This shape must be plotted by established points of
intersection. True radius settings for each element line
are taken from the front view and marked off on the
corresponding element line in the top view. These
points are connected with an irregular curve to give the
correct oval shape for the top surface. If the
development of the sloping top surface is required, an
auxiliary view of this surface shows its true shape.
Oblique Cone
An oblique cone is generally developed by the
triangulation method. Look at figure 8-16 as you read
this explanation. The base of the cone is divided into an
equal number of divisions, and elements 0-1, 0-2, and
so on are drawn in the top view, projected down, and
drawn in the front view. The true lengths of the elements
8-11
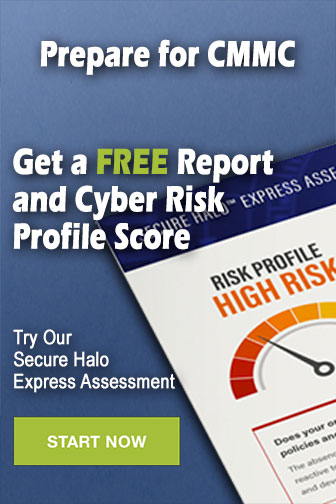