RADIUS (R)The radius of the bend. It is always
Where BA = bend allowance, N = number of
measured from the inside of the bend unless stated
degrees of bend, R = the desired bend radius, and T =
otherwise.
the thickness of the metal.
SETBACK (SB)The distance from the bend
tangent line to the mold point. In a 90-degree bend, SB
= R + T (radius of bend plus thickness of metal).
FLATThat portion not including the bend. It is
equal to the base measurement minus the setback.
BASE MEASUREMENTThe outside diameter
of the formed part.
Engineers have found they can get accurate bends
by using the following formula:
BA = N
0.01743
R + 0.0078
T
SHEET METAL SIZES
Metal thicknesses up to 0.25 inch (6mm) are usually
designated by a series of gauge numbers. Figure 8-5
shows how to read them. Metal 0.25 inch and over is
given in inch and millimeter sizes. In calling for the
material size of sheet metal developments, it is
customary to give the gauge number, type of gauge, and
its inch or millimeter equivalent in brackets followed by
the developed width and length (fig. 8-5).
TYPES OF DEVELOPMENT
A surface is said to be developable if a thin sheet of
flexible material, such as paper, can be wrapped
smoothly about its surface. Therefore, objects that have
plane, flat, or single-curved surfaces are developable.
But a surface that is double-curved or warped is not
considered developable, and approximate methods must
Figure 8-5.Reading sheet metal sizes.
be used to develop it.
Figure 8-6.Development of a rectangular box.
8-4
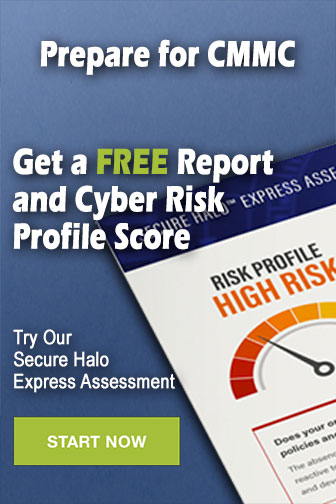