Tolerances
Introduction
Quality and accuracy are major considerations in making machine parts or
structures. Interchangeable parts require a high degree of accuracy to fit
together. Dimensions of parts given on blueprints and manufactured to those
dimensions should be exactly alike and fit properly. Unfortunately, it is
impossible to make things to an exact or dimension. Most dimensions have a
varying degree of accuracy and a means of specifying acceptable limitations
in dimensional variance that an object will tolerate and still function.
Tolerance
Tolerance is the total amount a specific dimension may vary stated as a
minimum and maximum limitation.
Tolerancing
definitions
To understand tolerances, you should understand some of the definitions
associated with the determination of a tolerance. These definitions may be
generally categorized as relating to size, allowance, or fit.
SIZE: The size of an object or its mate is known as nominal, basic, or design
size.
ALLOWANCE: The maximum and minimum allowable dimensions are
known as limit, allowance, unilateral, and bilateral tolerances.
FIT: Fit, clearance, interference, or transition fit refer to how the object fits
an assembly.
Size
To specify the size of an object, you dimension it with a nominal size, basic
size, or design size.
NOMINAL SIZE: Nominal size generally identifies the overall size of an
object.
BASIC SIZE: The basic size is the decimal equivalent of a nominal or
numerically stated size. It is the dimension from which you derive the limits
of size by the application of allowances and tolerances.
Continued on next page
3-40
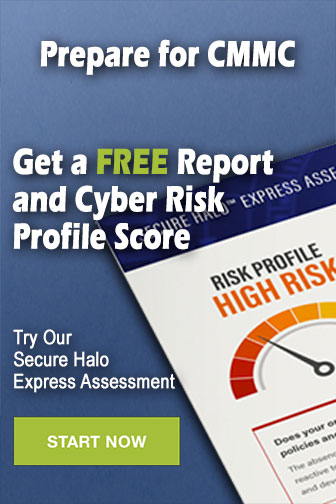